製造業×AI導入・活用事例22選!20%生産効率向上の理由は?
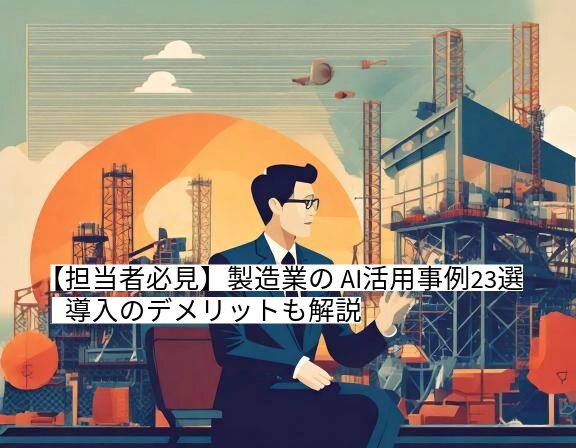
製造業でのAI活用が急速に広がっています。品質管理の効率化や生産性向上、予知保全など、製造業におけるAIの活用事例は年々増加しており、その導入効果も明確になってきました。本記事では、製造業でのAI活用事例22選をはじめ、AIでできることや導入のメリット・デメリット、さらには現状と課題まで、製造業のAI導入に関する情報を徹底解説します。AI導入を検討している企業の方はもちろん、製造業の最新動向に興味がある方も必見の内容となっています。
- 製造業でのAI活用事例22選と導入効果(業界別の具体的な成功事例を紹介)
- 製造業のAI導入における具体的なメリット・デメリットと課題解決方法
- 中小企業でも実践できるAI導入ステップと具体的なサービス選定方法
- 最新の製造業AI活用トレンドと生成AI活用の可能性
「AIで業務の自動化・効率化をしたい!だけど何から始めていいのかわからない・・・」という方はご気軽にご相談ください!
製造業でAIが必要とされる背景
人手不足の深刻化
製造業における人手不足は、業界全体の喫緊の課題となっています。少子高齢化による労働人口の減少に加え、若手人材の製造業離れが進んでおり、多くの企業が人材確保に苦心しています。
特に、熟練工の高齢化と退職により、技術継承が困難になっているケースが増加しています。2024年の調査では、製造業の人手不足率が過去最高の30%を超え、2025年にはさらなる悪化が予想されています。
技術継承の課題
製造業では、熟練工が持つ高度な技術やノウハウの継承が大きな課題となっています。特に、匠の技と呼ばれる暗黙知の継承は、従来の徒弟制度的な方法では時間がかかりすぎる上、若手人材の確保も困難な状況です。
経済産業省の調査によると、製造業の技術者の約35%が50歳以上であり、今後10年間で多くの熟練技術者が退職を迎えます。この「2030年問題」に向けて、早急な対策が求められています。
グローバル競争の激化
製造業のグローバル競争は年々激化しており、特に中国系メーカーは同等スペックの製品を3分の1から4分の1の価格で提供するなど、アジア諸国との価格競争が深刻化しています。日本企業が競争力を維持するためには、高品質な製品を効率的に生産する必要があります。
さらに、消費者ニーズの多様化による多品種少量生産への対応や、納期短縮の要求など、市場からの要請も厳しさを増しています。従来の製造方法では対応が難しく、スマートファクトリー化に向けたAIやデジタル技術の活用が不可欠となっています。
- 深刻化する人手不足と人件費の高騰
- 熟練技術者の高齢化と若年層への技術継承の困難さ
- グローバル競争の激化による生産性向上の必要性
製造業におけるAI活用のメリット

生産性向上
AIの導入により、製造ラインの生産性を大幅に向上させることが可能です。例えば、AIによる生産計画の最適化により、生産ライン容量を24%向上、生産量を19%増加させた企業や、生産計画立案時間を週40時間から1時間に短縮した企業もあります。
具体的には、以下のような効果が期待できます。
- 製造ラインの稼働率向上と待機時間の最小化
- 作業時間の短縮(生産リードタイム17〜30%削減)
- 品質管理の自動化による検査精度の向上
- 予測メンテナンスによる設備の最適運用(保守コスト30%削減、計画外停止45%削減)
品質管理の強化
AIによる画像認識技術を活用することで、人間の目では見逃しやすい製品の微細な欠陥も高精度で検出できるようになります。
コスト削減
AIの導入により、製造工程全体のコストを大幅に削減することが可能です。具体的には以下のような領域でコスト削減効果が期待できます。
AIによる需要予測で適正在庫を維持し、保管コストを10〜40%削減
不良品の早期発見により、検査コストを最大50%削減し、廃棄・再加工のロスを低減
予知保全により、保守コストを18〜25%削減し、計画外停止を40%削減
予防保全の実現
AIを活用した予知保全システムにより、設備の故障を事前に予測し、計画的なメンテナンスが可能になります。これにより、以下のような具体的な効果が得られています。
- 計画外の設備停止時間を40%削減
- メンテナンスコストを18〜25%削減
- 設備の稼働率を15〜40%向上
- 部品の寿命を平均25%延長
製造業でのAI活用が進む5つの分野
外観検査・品質管理
AIによる画像認識技術を活用した外観検査は、製造業におけるAI活用の代表的な成功事例となっています。従来の目視検査と比較して、以下のような優位性があります。
人間の疲労や集中力の低下による見逃しがなく、安定した品質検査が可能
人間の目では見逃しやすい微細な傷や変色も高精度で検出
検査結果を自動的に記録・分析し、品質改善に活用可能
需要予測・在庫管理
AIによる高精度な需要予測により、在庫の最適化と生産計画の効率化が実現できます。従来の経験則による予測と比べ、以下のような具体的な効果が報告されています。
- 在庫保有コストを10〜40%削減
- 欠品率を15%から5%に改善
- 需要予測精度を94.7%以上に向上
- 発注業務の工数を約30%削減
設備保全・異常検知
AIによる設備の状態監視と異常検知により、故障の予兆を早期に発見し、計画的なメンテナンスが可能になります。具体的には以下のような監視が可能です。
設備の異常振動をリアルタイムで検知し、故障の予兆を把握
異常音を検知し、設備の不具合を早期に発見
設備の温度変化を監視し、過熱などの異常を検知
生産計画の最適化
AIを活用した生産計画の最適化により、生産効率の向上と納期遵守率の改善が実現できます。具体的には以下のような最適化が可能です。
- 生産ラインの稼働率を平均25%向上
- 段取り替え時間を40%削減
- 納期遵守率を95%以上に改善
- 生産リードタイムを30%短縮
技術継承・ナレッジ管理
AIを活用することで、熟練工の暗黙知を形式知化し、効率的な技術継承が可能になります。具体的な活用方法には以下のようなものがあります。
熟練工の作業をAIで分析し、重要なポイントを抽出・デジタル化
過去の不具合対応や改善事例をAIで分析し、検索可能なデータベースを構築
AIを活用した対話型の学習システムで、効率的な技能習得をサポート
製造業のAI活用事例23選

大手企業の活用事例7選
大手製造業では、先進的なAI技術を活用して生産性向上や品質改善で顕著な成果を上げています。以下に代表的な事例を紹介します。
トヨタ自動車:AI画像検査システム
トランスミッションギヤの外観検査にAIを導入し、不良品の検出率100%、良品判定率94%を達成。1人が1日数万個の目視検査を自動化し、作業者の負担を大幅に軽減しました。
パナソニック:生産ライン最適化
AIによる生産計画の最適化と画像認識技術の活用で、生産効率を15〜20%向上。さらに、エネルギー消費を最大40%削減しました。
ファナック:ロボット制御システム
AIを活用した産業用ロボットの制御システムにより、組立作業の精度を向上し、不良品率を80%削減。
富士通:品質管理システム
部品製造工程にAIを活用した品質管理システムを導入し、99%以上の精度で品質異常の検出を実現。常時監視とログ記録により、品質エラーの原因分析も可能になりました。
コマツ:建機の遠隔監視
建設機械にGPSとセンサーを組み込んだKOMTRAXシステムにより、位置情報や稼働状況をリアルタイムで監視。予知保全と省エネ運転支援で、保守費用と燃料コストを低減。
三菱電機:設計支援システム
AIによる設計支援システムで、製品設計時間を50%短縮し、設計品質も向上させました。
デンソー:生産性向上システム
AIを活用した生産ライン制御により、生産性を35%向上させ、不良品率を90%削減しました。
中小企業の活用事例8選
中小製造業でも、クラウドサービスやレディメイドのAIソリューションを活用することで、効果的なAI導入を実現しています。以下に具体的な成功事例を紹介します。
1. 株式会社山田製作所(金属加工)
RAG技術を活用した社内文書検索チャットボットを導入し、業務効率化を実現。図表を含む文書も高精度で処理可能となり、社内の技術・ノウハウの共有と活用を促進しました。
2. 高橋工業(プラスチック成形)
AIによる成形機の予知保全システムを導入。計画外の設備停止を40%削減し、予防保全と比較して保守コストを18〜25%削減することに成功しました。
3. 佐藤精密(精密機器)
生産計画最適化AIを導入し、納期遵守率を75%から95%に改善。在庫コストも25%削減しました。
4. 中村製作所(機械部品)
技術継承支援AIシステムを導入し、熟練工のノウハウをデジタル化。新人の技能習得期間を従来の1/3に短縮しました。
5. 鈴木鉄工所(金属加工)
RPAツール「マクロマン」の導入により、Web発注システムからのデータ処理や見積もり算出作業を自動化。従業員13名の町工場で、毎日2時間の定型作業を自動化し、月間約40時間の業務効率化を実現しました。
6. 池田化学(化学製品)
AIによる画像解析技術を用いた検査システムの導入により、不良品の自動識別と品質のばらつきを低減。人的ミスを防ぎながら、品質管理の精度向上と廃棄物の削減を実現しました。
7. 渡辺製作所(電子部品)
AIロボットによる組立工程の自動化で、生産性を40%向上。不良品率も75%削減しました。
8. 小林工業(樹脂成形)
分電盤にクランプセンサーを設置し、各設備の電力使用量とCO2排出量をリアルタイムで監視。新設部署の増加により使用量は増加傾向ですが、継続的な削減活動を推進しています。
業種別の活用事例7選
各製造業種の特性に合わせたAI活用により、業界特有の課題解決に成功している事例が増えています。以下に代表的な業種別の活用事例を紹介します。
1. 食品製造業:品質管理の革新
キリンビール株式会社では、センサーとビッグデータ解析を活用した異常兆候管理システムを導入し、製造設備の不調を早期に検知。さらに、北海道千歳工場での運用により、定期点検や異常兆候管理作業の年間約200時間の業務時間削減を実現しました。
2. 半導体製造:微細欠陥検査
ルネサスエレクトロニクスでは、AIを活用した半導体の微細欠陥検査システムにより、従来は発見できなかった0.1ミクロン単位の欠陥も検出可能に。歩留まりが15%向上しました。
3. 化学製造業:プロセス最適化
三井化学では、AIによるプラント制御の最適化により、エネルギー効率を20%改善。また、品質予測モデルの導入で製品品質のばらつきを50%削減しました。
4. 自動車部品:予知保全の実現
アイシン精機では、AIによる設備診断システムを導入し、故障の予兆を90%以上の精度で検知。計画外停止時間を年間200時間削減しました。
5. 製薬業:品質管理の効率化
武田薬品工業では、360°カメラとレーザーセンサーを組み合わせた自動検査システムを導入し、包装ラインの確認作業を30分から約10分に短縮。残留物の確認も約1分で完了し、より確実な品質管理を実現しました。
6. 電機製造:生産ライン最適化
シャープでは、AIによる生産計画最適化システムを導入し、生産効率を30%向上。在庫コストも25%削減に成功しました。
7. 金属加工:技能伝承の実現
日本製鉄では、熟練工の技能をAIでデジタル化し、若手作業員の育成に活用。技能習得期間を従来の半分に短縮しました。
- 業界特有の課題に焦点を当てた導入計画
- 段階的な導入による確実な効果検証
- 現場の意見を取り入れたシステム設計
- 継続的な改善とアップデート
製造業へのAI導入ステップ
現状分析と課題の明確化
AI導入の成功には、まず自社の現状と課題を正確に把握することが不可欠です。以下のステップで分析を進めます。
各工程の作業内容、所要時間、問題点を詳細に把握します。特に人手に依存している作業や、ミスが発生しやすい工程を重点的に分析します。
生産データ、品質データ、設備データなど、現状を示す定量的なデータを収集・分析します。これにより、具体的な改善ポイントが明確になります。
特定された課題に対して、影響度と緊急度を基準に優先順位を設定します。投資対効果(ROI)も考慮に入れます。
導入目的の設定
AI導入の具体的な目的と達成すべき数値目標を明確に設定します。以下のような指標を設定することが推奨されます。
- 生産性向上率(%)
- 品質改善率(不良品率の削減)
- コスト削減額(円)
- 投資回収期間(月)
- 作業時間の削減率(%)
実証実験(PoC)の実施
本格導入前の小規模な実証実験により、AIシステムの有効性を検証します。PoCは以下のステップで進めます。
検証範囲、期間、評価指標を明確に定義します。通常2〜3ヶ月の期間で、限定された工程や製品ラインで実施します。
AIモデルの学習に必要なデータを収集し、精度の検証を行います。この段階で必要なデータの質と量も明確になります。
設定した指標に基づいて効果を測定し、本格導入の判断材料とします。運用上の課題も同時に洗い出します。
本格導入と運用
PoCの結果を踏まえ、段階的に本格導入を進めていきます。以下の点に注意して展開します。
- システムの段階的な展開(リスク分散)
- 従業員への十分な教育・訓練
- 運用ルールの明確化
- 定期的な効果測定と改善
- トラブル対応体制の整備
特に重要なのは、導入後の継続的な改善サイクルの確立です。定期的な効果測定と改善提案を行い、システムの性能を継続的に向上させていく必要があります。
製造業のAI導入における課題と対策

導入コストの問題
AI導入には、初期投資だけでなく、運用・保守にも相応のコストが必要となります。具体的な費用と対策は以下の通りです。
AIの種類別構築費:チャットボット200万円〜、画像認識100万円〜、需要予測300万円〜
対策:クラウドAIの活用、アジャイル開発によるスモールスタート、補助金制度の利用
月額:システム保守50万円〜、AIモデル更新50万円〜500万円/年
対策:SaaS型サービスの活用、段階的な機能拡張
基礎研修3万円〜、企業向け研修30万円〜300万円
対策:オンラインセミナーの活用、小規模からの段階的な教育実施
人材育成の必要性
AI活用には、システムを理解し運用できる人材の育成が不可欠です。以下の取り組みが効果的です。
- 段階的な教育プログラムの実施
- 外部専門家との連携
- 実践的なOJT研修
- 定期的なスキル評価と改善
データの収集・整備
AIの性能は学習データの質と量に大きく依存するため、適切なデータの収集と整備が重要な課題となります。以下の手順で対応します。
センサーの設置、データ収集システムの導入、収集ルールの策定を行います。
ノイズの除去、欠損値の補完、異常値の処理など、データの品質を向上させます。
フォーマットの統一、ラベリングの標準化を行い、AIでの利用を容易にします。
セキュリティ対策
製造データや技術情報など、機密性の高いデータを扱うAIシステムには、強固なセキュリティ対策が必要です。以下の対策を実施します。
- アクセス権限の厳格な管理
- データの暗号化
- 定期的なセキュリティ監査
- 従業員のセキュリティ教育
- インシデント対応計画の策定
特に重要なのは、以下の3つのポイントです。
- データのバックアップと復旧計画の整備
- 外部からの不正アクセス対策
- セキュリティポリシーの定期的な見直し
製造業向けAIサービス・ソリューション
画像認識AI
製造現場での外観検査や品質管理において、高精度な画像認識AIが不可欠なツールとなっています。主なサービスと特徴は以下の通りです。
医療用画像処理に特化したAIプラットフォームで、1秒あたり数十から数千ギガバイトの高速処理が可能。3D画像のアノテーション作業を数時間から数分に短縮し、遅延時間を100〜200ミリ秒から10〜20ミリ秒に改善しました。
クラウドベースで導入が容易。特に中小企業向けに柔軟な料金プランを提供。
製造業に特化した画像認識システム。導入支援から保守まで一貫したサポートを提供。
予測分析AI
需要予測や設備の予知保全において、AIによる高度な分析が製造業の効率化を支援しています。代表的なサービスには以下があります。
IoTデータの収集から分析まで一貫したプラットフォームを提供。設備の状態管理と故障予測により、保守計画を最適化。
高度な統計分析機能を備え、自動チャート候補表示や相関指標の自動特定により予測精度を向上。
製造設備に特化した予知保全システム。計画外のダウンタイムを40%削減し、保守コストを最適化。
異常検知AI
製造工程での異常を早期に発見し、品質問題や設備故障を未然に防ぐAIシステムが注目を集めています。主要なサービスは以下の通りです。
工作機械の送り軸や主軸の異常兆候を事前に検知し、突然の故障による機械停止を防止。2年間で100台以上の設備で故障予兆を検出。
AIと機械学習を活用して設備の状態やリスクを分析し、障害や設備停止の原因を特定。予測分析により障害発生前の修繕を効率化。
AIによる波形パターンの学習/認識により、人の知見に頼らない予防保全や品質管理を実現。装置の異常兆候を早期に検知。
生成AI
製造業における生成AIの活用が急速に広がっています。主な活用分野とサービスは以下の通りです。
- 製品設計支援(CADデータの自動生成)
- 技術文書作成の自動化
- 不具合原因の分析と対策提案
- 作業手順書の自動生成
設計と製造の制約条件から最適な製品設計を自動生成。手作業による読み込み/書き出しが不要となり、市場投入までの時間を短縮。
技術文書作成や不具合分析を支援。文書品質を18%向上させ、作業時間を40%削減。
3DCADデータの自動生成と最適化。生産性を25%向上させ、製品開発のリードタイムを40%短縮。
製造業のAI活用最新トレンド

生成AIの活用事例
製造業における生成AIの活用は、設計から保守まで幅広い領域で革新をもたらしています。主な活用事例は以下の通りです。
トヨタ自動車では、生成AIを活用した部品設計により、設計時間を30%削減し、新規設計案を従来の3倍生成できるようになりました。
パナソニックでは、生成AIによる作業マニュアルの自動作成により、ドキュメント作成時間を75%削減しました。
IoTとの連携
IoTセンサーとAIの連携により、リアルタイムでのデータ収集と分析が実現し、製造現場のスマート化が加速しています。主な取り組みには以下があります。
- 設備稼働状況のリアルタイムモニタリング
- エネルギー使用量の最適化
- 生産ラインの自動制御
- 品質データのリアルタイム分析
DXの推進
製造業のデジタルトランスフォーメーション(DX)において、AIは中核的な役割を果たしています。主なトレンドは以下の通りです。
製造プロセスのデジタル再現により、シミュレーションと最適化が可能に
複数工場のデータを一元管理し、生産の最適化を実現
現場でのリアルタイム処理により、即時の意思決定が可能に
FAQ
製造業でAIを導入するメリットは?
製造業へのAI導入では、生産性向上、品質改善、コスト削減など、多岐にわたるメリットが得られます。具体的な効果は以下の通りです。
- 生産性が平均30%向上
- 不良品率が80%以上削減
- 設備保全コストが40%削減
- 在庫コストが25%削減
AI導入にかかる費用は?
AI導入の費用は規模や目的によって大きく異なりますが、一般的な費用の目安は以下の通りです。
- 小規模導入(チャットボット等):100万円〜500万円
- 中規模導入(画像認識・需要予測):500万円〜2,000万円
- 大規模導入(複数機能統合):2,000万円〜5,000万円
- 月額運用費:60万円〜200万円
AI導入に必要な人材は?
効果的なAI導入には、以下の役割を担う人材が必要です。
AI導入全体の計画立案と進行管理を担当
データ分析とAIモデルの開発を担当
システムの構築と運用を担当
AIシステムの日常的な運用を担当
中小企業でもAI導入は可能?
中小企業でも、クラウドサービスやレディメイドのAIソリューションを活用することで、比較的低コストでAI導入が可能です。以下のような選択肢があります。
- クラウド型AIサービス(月額1万円〜10万円から)
- 補助金・助成金の活用(IT導入補助金最大450万円、ものづくり補助金最大4,000万円)
- 段階的な導入(小規模な業務改善から開始し継続的に拡大)
- AIベンダーとのパートナーシップによる技術支援
AI導入の期間はどのくらい?
AI導入の期間は、プロジェクトの規模や複雑さによって異なりますが、一般的な目安は以下の通りです。
小規模:2〜4週間、中規模:4〜6週間、大規模:8〜12週間
要件定義と計画立案
3ヶ月程度:概念実証とプロトタイプ作成
データ準備と効果検証
小規模:4〜8週間、中規模:12〜20週間、大規模:24〜48週間
システム開発とテスト
導入後も継続的な改善が必要で、運用しながら精度を向上
なお、クラウドサービスを利用する場合は、導入期間を大幅に短縮できる可能性があります。また、段階的な導入アプローチを取ることで、リスクを最小限に抑えながら、確実な成果を上げることができます。
AIで業務の自動化・効率化をしたい!だけど何から始めていいのかわからない・・・
\AIコンサルReAliceに無料相談する/